Global reporting of accidents and near misses when using powered access equipment for temporary work at height is helping to inform campaigns, guidance and training from the International Powered Access Federation (IPAF), aimed at making the equipment safer to use than ever.
Features
How building a culture of collaboration and transparency is making powered access safer
Culture has such an important role in safety – one that often goes unrecognised. When things go wrong and accidents occur, organisations with unhealthy cultures can tend to focus on who’s to blame.
But pointing the finger doesn’t help to make workplaces safer. In fact, it’s more likely to foster a negative atmosphere and create a climate that incentivises workers to cover their tracks following an incident or near miss.
Collaborative learning project is leading to a reduction in the most serious incidents. Photograph: IPAF
Transparency, openness and a willingness to learn from mistakes are crucial elements in developing workplace cultures able to change and adapt in the name of safety.
Here at the International Powered Access Federation (IPAF) we’re proud to have spent more than a decade building a global movement dedicated to learning from incidents and using data to identify risks and take preventive action.
As the not-for-profit members’ organisation for the powered access industry, we have pooled knowledge and insights from manufacturers, rental companies, contractors and users to build a worldwide picture that is helping us to reduce injuries and fatalities.
At the time of writing, up to December 2023, we have seen a 21 per cent year-on-year increase in the number of incident reports we have received from users of powered access equipment for work at height – more than 930 from 40 countries.
And although more incidents (whether they be accidents or near misses) might seem like a bad thing, we have also seen a 3.6 per cent reduction in fatalities – an indication that this collaborative learning project is leading to a reduction in the most serious incidents.
Benefits of analysing incident data
So how do we use this data to reduce incidents? The global trends we can identify in the data inform every aspect of our work, from our training programmes to rental supplier audit criteria and the issues we communicate to our members.
To quote our chief executive and managing director, Peter Douglas: “Accident reporting is our most important initiative – it drives all the other initiatives.”
Every year, IPAF analyses trends in the data and identifies a Global Safety Campaign targeted at a specific type of risk or incident outcome, emphasising the importance of working safely to mitigate specific concerns and avoid certain types of incidents when using mobile elevating work platforms (MEWPs).
Every year IPAF analyses trends in the data. Photograph: IPAF
MEWPs come in a range of shapes and sizes, with categories including scissor lifts, articulated booms, truck-, track- and van-mounted booms, and mast-climbing devices. Although there are commonalities between them, each kind of MEWP comes with its own specific risks that must be understood by their operators.
This year, the focus has been directed at risks associated with working near power lines through our ‘High Voltage!’ campaign.
We launched the campaign after our Accident Reporting Portal revealed a notable increase in incidents involving electrocutions and electric shocks associated with power lines since 2015.
About the High Voltage! campaign
Our High Voltage! safety campaign identifies the hazards and risks associated with working near power lines and explains how to work safely to avoid the risks.
What are the hazards and risks?
If a MEWP or its occupants come into contact with power lines the result can be instant death, electric shock, or other injuries caused directly or indirectly by electricity.
Electric shock can also occur without direct contact with power lines as arcing or flashover may result if a MEWP is closer to the power line than a minimum of 3 metres or 10 feet.
Incorrect identification of overhead power lines is also a risk as they can be mistaken for telecommunication lines. Other risk factors include power lines that may be hidden from view by vegetation or trees, a lack of work site supervision and operator complacency.
Our key safety messages
The campaign featured four key messages to reduce the risk of electrocutions and shocks:
- Plan thoroughly
Look out and around for power lines in the work area. Conduct a site survey and risk assessment ensuring a safe system of work (SSoW) is completed. Correct machine selection is critical. If power lines are in your work area contact the Energy Supply Authority (ESA) before work commences. Ensure all operators are briefed prior to commencement of work and that they are made aware of the presence of power lines in the vicinity.
- Ensure operators are trained
Anyone involved in the safe use of MEWPs must be properly trained on the MEWP they are using and must have received a machine-specific familiarisation. As this is a high risk activity and can have severe consequences, managers must ensure MEWP operators, supervisors and spotters are briefed on the SSoW.
- Stay outside exclusion zones
An exclusion zone is the prescribed safety envelope around live electric power lines (minimum of 10 feet for operators). You must not operate a MEWP where there is potential for any part of it to enter an exclusion zone. Distances for exclusion zones can vary; these must be obtained from the relevant ESA.
- Know your rescue plan
If someone has been electrocuted by arcing of electricity or has been in contact with a power line, call the emergency services immediately and call the ESA to have the power turned off.
The rescue plan
It was important that we provided clear and easy-to-remember guidance that our members could act on in the event of an incident. We summarised this as STAY – CALL – WAIT.
STAY
if you are in the platform, stay there. If you are on the ground, do not approach the MEWP and remain a safe distance away as recommended by the ESA.
CALL
the emergency services.
WAIT
for assistance from the emergency services and ESA.
The bigger picture
Alongside our annual Global Safety Campaign, we work closely with industry colleagues to ensure ongoing dialogue on safety issues and encourage a collective goal of continuous improvement.
While our flagship campaign will focus on one specific area, we know from experience and the data we hold that working at height and use of powered access equipment carries numerous and varied risks.
These range from the obvious risk of falls from height to lesser-known dangers such as working near radio frequency (RF) sources.
We provide guidance on a broad range of safety issues, with resources including ‘toolbox talk’ discussion prompts for use during team briefings alongside additional materials such as posters and videos.
Training programmes and accreditation schemes, such as IPAF Rental+, are reviewed regularly to ensure the latest best practice is followed.
Our engagement work on safety aims to reach manufacturers, rental companies, contractors and end users to engender an industry-wide culture of safety.
All of this work is encapsulated in our annual Global Safety Report. The 2023 edition took a deep dive into the top six reasons for fatal and serious incidents, drawing on our incident data to provide a detailed and evidenced snapshot of areas of risk.
Key areas of focus this year included the electrocution risks highlighted in the High Voltage! campaign alongside other emerging issues such as the increase in incidents involving type 1b static boom MEWPs.
None of this work would be possible without the collaborative and open culture that we have fostered within our industry – by working together and focusing on learning opportunities we are making our industry safer.
Safety in the spotlight: Safe loading
Responding to a request from the IPAF UK Country Council, we launched a UK campaign on safe loading, unloading and transportation of MEWPs.
Over a 10-year period IPAF received more than 1,200 reports involving delivery drivers from 21 countries. Sadly, these reports included 16 fatalities.
IPAF issued guidance to prevent incidents during loading, transport and unloading. Photograph: IPAF
In response we issued key guidance to prevent incidents during loading, transport and unloading. The goal was to encourage drivers to maintain an ongoing awareness of the risks, even when carrying out tasks that might be considered routine.
Our advice was:
- Prepare a risk assessment – ensure this is completed ahead of any MEWP loading/unloading activity. Observe IPAF guidance when loading or unloading on or adjacent to roads.
- Manoeuvre with care – take care when loading/unloading MEWPs and ensure drive orientation is confirmed at all times. Contact or collision with an object or person is the main cause of this type of incident.
- Be mindful of tip-over risk – ensure ramps are adjusted according to the MEWP being loaded.
- Minimise pedestrian control – driving the MEWP from outside the platform should be kept to an absolute minimum. For instance, when manoeuvring through narrow doorways or under low ceilings. Operators/drivers should be spatially aware of their surroundings. Correct drive orientation must be confirmed at all times.
- Avoid slips, trips and falls – ensure the bed of the vehicle is clear of debris and any edge protection. Ensure fall prevention systems are used as per the risk assessment.
- More information about the campaign is available on the IPAF website:
Brian Parker is head of safety & technical at IPAF
More information about the campaign is available on the IPAF website: ipaf.org
FEATURES
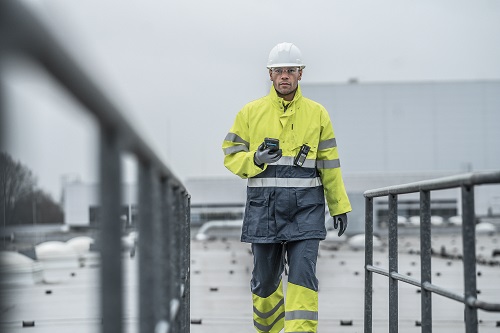
Gas detection – the rise of smart systems
By Becca Dodds, Draeger Safety UK on 26 August 2025
Mobile and fixed gas detectors have long been a crucial tool for alerting workers to the presence of asphyxiating or explosive gases, but developments in smart and connected technology are making it much easier to monitor entire networks of detectors and respond immediately to alarms and emergencies that could pose a risk to life or site safety.
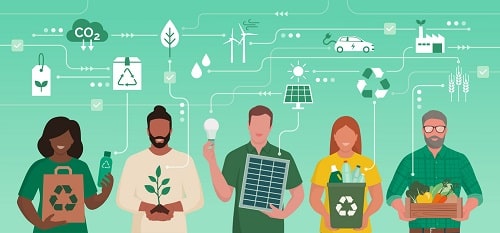
Changes to ISO management standards: start preparing now
By Dr Keith Whitehead, British Safety Council on 08 August 2025
The key ISO management standards setting out best practice frameworks for effectively managing occupational health and safety, environmental and quality risks and opportunities are undergoing major revision, so it’s essential businesses start planning now to meet the new requirements in order to maintain their certifications under the relevant standards.
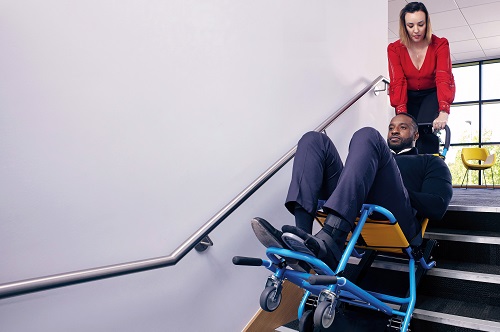
Inclusive, compliant evacuation planning: why training and maintenance matter
By Evac+Chair on 07 August 2025
Those responsible for business premises should provide assistive equipment to ensure the safe and efficient evacuation of people with mobility impairments. However, it is crucial that this equipment is regularly maintained and that staff are thoroughly trained in its use – otherwise, confusion and potentially fatal delays can arise in an emergency.