Developments in smart textiles offer new ways of protecting workers’ health and safety – such as clothing that can detect and warn of electrical dangers.
Features
Get smart: how textile technology can protect workers
Rules and regulations designed to ensure the safety of electricians at work are very strict, but electrical incidents – such as electric shocks and burns from contact with live circuits when working on fixed electrical installations in buildings – still happen.
In many countries, electrical incidents involving employees – such as a serious electrical burn – must be reported by law. However, in practice often only the most serious accidents, like major electric shocks or fires caused by an electrical overload in a building’s fixed electrical installation, are actually reported.
A smart textile system can automatically call for help if it detects an electrical emergency – like a voltage drop on the wearer’s body. Photograph: ADRESYS
In fact, analysis of electrical safety incidents at work in Austria, where ADRESYS is based, gives an idea of the extent of the problem that may exist in many countries. In Austria, which has a population of 8.8 million, the available statistics and research show that:
- On average there are six fatalities per year involving electricity at work
- There are approximately 140 electrical accidents at work in total per year
- Each electrical accident at work costs approximately 40,000 EUR
- Most of the injuries are caused by electric shocks, followed by electrical burns or ventricular fibrillation (a serious and life-threatening cardiac rhythm disturbance that prevents the heart pumping blood out to the body, and which can lead to cardiac arrest)
- Most of the electrical injuries are caused by contact with low voltage levels (i.e. a maximum of 250 volts).
However, it is thought that, due to under-reporting by employers, the actual number of electrical incidents and injuries at work in Austria is significantly higher¹². A similar situation is likely to exist in other countries.
What are smart textile systems?
A smart textile system (STS) is an assembly of smart components integrated into a textile, which can be used as STS clothing to be worn at work or in other settings, like sports and leisure.
An STS can have a variety of features and functions. These include the ability to send communication signals to a body-worn electronic device. For example, this can be information from the wearer’s body picked up by the STS clothing they are wearing – such as a lack of motion that could indicate they are incapacitated or have lost consciousness. An STS can also have an energy function – such as the capability to detect electrical voltages and currents that come into contact with the smart textile.
In short, an STS can collect, show and transmit information about the person wearing the STS clothing and their direct environment.
An STS used as workwear – especially for electricians – offers several safety benefits. Photograph: ADRESYS
One recent development in the field of STS is a smart textile that can detect both electrical incidents – such as a voltage drop or an electrical current flow through the body of the person wearing the STS – and a fall, such as from a ladder.
If the STS detects an electrical emergency – like a voltage drop on the wearer’s body that could result in an electric shock – it automatically calls for help.
The system consists of a shirt with integrated sensors, electrical conductors and a holder or cradle on the arm with a magnetic holder.
A data-processing unit with a communication function is securely attached to the holder on the arm using the magnets. Electrodes in the left and the right cuff of the shirt are continuously in contact with and monitor the skin of the wearer.
In the event of an electrical accident, the electrodes in the cuffs will immediately detect a voltage drop between the upper arms of the wearer. This indicates that a current is flowing through one of the two arms, and the system then immediately and automatically sends an emergency alert to pre-programmed contacts, so help can be sent.
The data-processing unit is powered by a rechargeable lithium-ion battery and connected to the user’s smartphone via a Bluetooth® connection. Once the alarm is received and raised, the unit automatically activates the rescue chain.
Prior to wearing the STS, the user stores their personal details and emergency contacts on an online portal. In the event of an electrical accident – or an incident like a fall – the system makes an emergency automated voice call and/or sends an SMS to summon help. The system can be programmed to send the alert to contacts such as an external emergency call centre or in-house first-aiders. The system also automatically provides the last known GPS location and data on the incident, such as whether it is an electrical accident or fall.
Sensors in the central control unit can also detect a fall and send an emergency alert requesting assistance.
The system also incorporates a manual alarm and task timer. These allow the person wearing the STS to manually call for help or an alarm to be automatically activated if the user does not acknowledge and they are safe, once a pre-set time period has passed.
The system is categorised as an ‘E-Com’ smart textile and belongs to the category of workwear for people working in dangerous electrical voltage environments.
The technology is undergoing further development. In the future it is expected that once the system detects a voltage drop between the user’s upper arms and a current flow through their body, it will be able to disconnect the electricity to the power source in question (like a machine an electrician is working on) to help prevent or avoid severe harm to the worker.
Smart workwear is more likely to be successful if the clothing can be washed and laundered in the same or a similar way as normal workwear. Photograph: ADRESYS
Developing an STS for workwear: the challenges
An STS used as workwear – especially for electricians – offers several safety benefits. By detecting electrical accidents and falls the rescue chain can be activated much earlier and severe harm can hopefully be avoided.
However, when used as general workwear, an STS provides additional functions and advantages. These include:
- The collection and procession of useful data – such as the exact location of the worker and the number of times the wearer comes into contact with an electrical current or suffers a fall
- Recording and collecting anonymous statistical data that can be used to build awareness – such as the actual number of times various workers wearing an STS come into contact with electrical currents or suffer falls
- Proactively detecting medical emergencies by measuring the wearer’s vital health parameters – such as their heart rate and breathing rate
- Saving lives – for example, by calling for help immediately in the event of problems like an irregular or unsafe heart rate.
However, while smart workwear offers promising possibilities for improving worker health, safety and wellbeing, there are many challenges around its development and roll-out at commercial scale.
The smart textile industry has to spend a lot of time and money researching, developing and creating prototypes of smart textiles and clothing and the actual creation and manufacture of an STS for full commercial roll-out at a reasonable scale and purchase price is challenging.
Although there is a market for smart textile components like sensors, actuators, conductive threads or cables, it is a major challenge to assemble these components in an STS that is durable, washable, reliable and cost-effective.
Another challenge is ensuring that these various components are compatible with each other when incorporated into smart textiles and smart clothing.
Developers of smart textiles have to ensure that the various components – such as sensors – can be integrated into the textile in a way that allows automated and mass production of the textile or garment. This includes finding ways to avoid the use of manufacturing and production processes that are impractical or costly for the textile industry, such as soldering and crimping.
Another challenge is ensuring that any smart textile used in workwear will meet the necessary requirements for durability, washability, certification standards and wearer comfort.
Most of the available smart textile products categorised as ‘E-Com’ are used in the health and sport sectors – for example, smart textiles and clothing capable of measuring and monitoring parameters like the wearer’s heart rate.
However, for those developing smart textiles, there are significant differences, requirements and challenges between sportswear and workwear.
For example, although a sports shirt is usually worn for just a handful of hours, a workwear shirt is generally worn for at least eight hours a day. This means the workwear shirt generally has to offer a higher level of wearer comfort.
In addition, workwear has to be capable of withstanding greater wear, tear and stress than most sportswear. This includes sweat, dirt, and mechanical abuse, such as the risk of abrasion or tearing of the textile.
When developing smart textiles for workwear there are also challenges around washing and laundering the clothing, without damaging the integrated components, like the sensors.
In general, most standard, ‘non-smart’ workwear is washed at 60°C in domestic washing machines or even industrially washed.
However, for smart textile products it is usually recommended that washing takes place at 30°C or lower, in a laundry bag, turned inside out, or in line with similar strict rules, to avoid damage to the textile and components.
Therefore, the development and launch of a range of smart workwear is more likely to be successful if the clothing can be washed and laundered in the same or a similar way as normal workwear.
As a result, another challenge that must be overcome is ensuring smart workwear can be properly and effectively laundered to a good standard without damaging its components.
Developing suitable processes for mass production of an STS
When developing the smart textile shirt that can help protect the wearer and raise the alarm if they are exposed to electrical danger, the developers worked with partners to evaluate which components would provide the desired functionality while being suitable for mass production in clothing.
The overall goal was to develop an STS that offers reasonable reliability, durability and washability. Field tests were carried out with over 100 electricians to identify the real-life conditions the STS would have to withstand when used as workwear.
The biggest challenges included ensuring that any manual work required in a factory to assemble and manufacture the smart textile clothing system and its components was kept to a minimum and ensuring the STS offered 100 per cent insulation.
Full insulation of the components such as the electrodes and the conductive cable that connects the sensors to the control unit on the arm is essential to avoid problems like mini-short circuits in the system and false alarms when there is no electrical danger to the wearer.
Full insulation of the STS also prevents the components from suffering corrosion due to exposure to chemicals in detergents during washing and laundering.
Washing stability and durability
As stated, workwear generally needs to be capable of withstanding quite rigorous washing and laundering.
So, tests needed to be carried out to ensure that the different materials, components and electric contact points in the smart textile shirt for electrical emergencies could withstand washing and laundering to an appropriate standard.
The extensive washing tests showed that the smart textile shirt and its components can withstand up to 50 washing cycles at 40°C in a domestic washing machine.
Standardisation and certification
For personal protective equipment (PPE), such as safety clothing like high visibility jackets and trousers, there are detailed official standards, certifications, and tests that manufacturers must follow. For PPE manufacturers, these provide a crucial guide so they can ensure their PPE provides the required level of protection and can be certified and sold on the market.
If the PPE meets these standards and certifications, it also provides assurance to the customer that they are purchasing approved, tested, and suitable PPE that will provide the publicly stated level of protection.
However, for an STS in general, very few official standards and certifications have been developed and introduced, that manufacturers can have their smart clothing approved under.
As a result, it can be difficult for an STS, including those designed to help protect workers’ health and safety, to be accepted by customers, as it may not be certified to a formal standard or certification, as they have not yet been introduced.
Some standards for smart protective clothing are currently being developed by working groups of Comité Européen de Normalisation (CEN). However, detailed and extensive test methods, quality assurance procedures and requirements for the washing durability and electrical insulation of the clothing have yet to be developed and introduced.
As a result, designers and producers of an STS for workwear often have to develop their own equipment and tests to check the functioning and quality of the STS. For example, for the smart textile shirt for electricians, the developer designed a special device so the electrical functionality of the shirts could be easily tested at the clothing manufacturing site. This avoided the need to use other special types of test equipment.
Conclusion
An STS designed for electricians can ensure help is summoned quickly in an electrical or other emergency.
However, developing, refining and improving an STS for electricians that provides reasonable reliability, durability and washability has been – and continues to be – a complex and challenging process. The developers must meet the requirements of protective clothing standards and satisfy the demands of the market and the end customers. The right electrical components must be found, assembled, integrated and connected to create an STS that can be manufactured in a cost-effective and automated process.
Nevertheless, despite these major challenges, STSs used in workwear have great potential for improving the health and safety of workers.
Johannes Bosch is sales expert for Northern Europe and UK at ADRESYS.
FEATURES
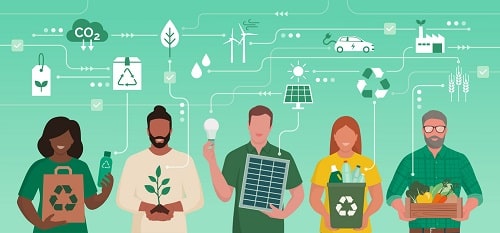
Changes to ISO management standards: start preparing now
By Dr Keith Whitehead, British Safety Council on 08 August 2025
The key ISO management standards setting out best practice frameworks for effectively managing occupational health and safety, environmental and quality risks and opportunities are undergoing major revision, so it’s essential businesses start planning now to meet the new requirements in order to maintain their certifications under the relevant standards.
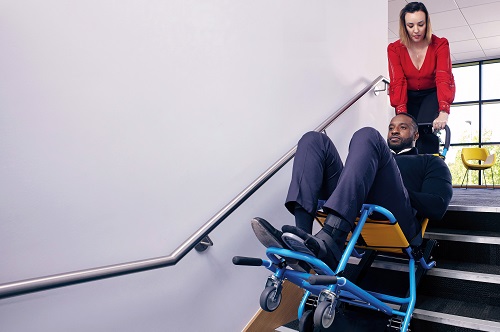
Inclusive, compliant evacuation planning: why training and maintenance matter
By Evac+Chair on 07 August 2025
Those responsible for business premises should provide assistive equipment to ensure the safe and efficient evacuation of people with mobility impairments. However, it is crucial that this equipment is regularly maintained and that staff are thoroughly trained in its use – otherwise, confusion and potentially fatal delays can arise in an emergency.
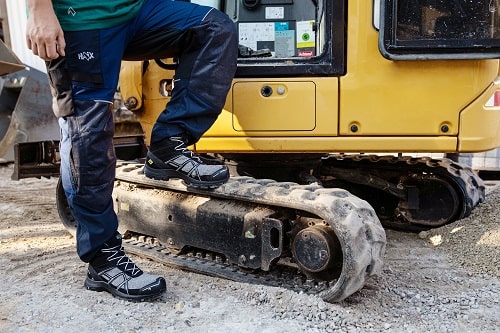
A step ahead: how the right safety footwear reduces workplace slips, trips and falls
By Simon Ash, HAIX on 06 August 2025
Safety footwear can prevent slip, trip and fall injuries, but it’s essential to consider other factors that could positively or negatively affect wearer comfort, such as breathable materials, waterproof qualities and boot weight.