An effective risk assessment is crucial in identifying significant danger to workers’ health and safety. However, there are some common pitfalls to avoid so the risks are properly identified and correctly managed.
Features
Six pitfalls to avoid in risk assessment
Risk assessment is the bedrock of good health and safety management, as they say. However, I would go a step further to say that risk assessment is the ‘heart of health and safety’. If we don’t get the risk assessment process right, we will falter on our overall efforts to effectively manage the significant risks to workers’ health, safety and wellbeing.
Here, I summarise the pitfalls under six main headings. These are lessons that I have learned, both as an experienced health and safety practitioner and from the various health and safety audits that I have carried out in my role as head of audit at British Safety Council India, overseeing the audits of the health and safety management systems of Indian businesses.
1. Line of sight missing from health and safety risk management – from the strategic level to site/operational level, and in the reverse direction
For highly hazardous operations, it is important that risks related to health and safety sit at strategic level and there is a clear line of sight (both ways) of this set of risks from the strategic level to the operational level at the site.
It is important for senior operational staff at the site to understand in what form and shape the risks related to health and safety (such as contractors’ work, fire risks or a hazardous gas leak) sit in the corporate office and at the board level.
Are they both aligned and how is it reviewed? Is it in a) an internal audits system b) a legislative review process c) the risk management committee or d) is it sitting as an enterprise risk?
A common mistake is failing to first attempt to substitute the hazard with something that is less hazardous. Photograph: iStock
2. Failing to identify all the hazards
If we focus solely on the obvious and visible hazards, we may fail to identify and take action on major hazards that pose a serious risk to workers’ health and safety.
For example, the safety of employees who drive as part of their work is very important, as the number of road traffic accidents in India is very high. However, it has been observed that the risks faced by those driving for work purposes have been overlooked by some organisations when carrying out and reviewing their risk assessments.
3. Hierarchy of controls not followed
Many times we have come across training and personal protective equipment (PPE) being mentioned as control measures. However, these are low in the hierarchy of controls and more effective control measures – such as substitution and engineering controls – should be considered first.
4. The risk level is not brought down to as low as reasonably practicable
It has not been uncommon for me to observe that dozens of residual risks sit as ‘high risk’. It is essential that residual risks are at ALARP (as low as reasonably practicable) and at an acceptable level.
If they continue to be in the ‘high’ category (and they can be in the ‘high’ category for a limited time only), then those risks need to be part of the review process at the highest level, until such time they are brought down to ALARP level.
5. Health and wellbeing overlooked in the risk assessment process
There is a tendency among some businesses to focus solely on safety hazards and to neglect health and wellbeing hazards. The health risks posed by working in hot, noisy, gaseous and uncomfortable environments must be assessed and controlled.
There is also an increasing focus on ensuring the wellbeing of workers and this needs to be included in the risk assessment.
Wellbeing includes workers’ physical, mental and emotional health and the associated areas of stress, anxiety and depression. These areas should be addressed in the health risk assessment.
Also, employers should assess and control the health effects of exposure to chemicals, radiation and vibration and work with display screen equipment, to name a few health hazards.
There is also an increasing focus on ensuring the wellbeing of workers and this needs to be included in the risk assessment
6. Live document and regular review of the risk assessment
Risk assessment is a dynamic process, especially for construction and process-related activities.
In construction, the look, form and shape of a construction site changes every other week. The risk assessment therefore needs to be very dynamic and the risks and hazards must be reviewed much more frequently than they would be for the normal operation in a running factory or a warehouse or a building/facility service. The need for a review emerges from i) occurrence of an incident ii) new applicable legislative requirements iii) changes in process/equipment and iv) large-scale change of people/person change in a critical operation.
Conclusion
It is important to keep the risk assessment and management process simple. Risk assessment and management are easier to manage when they are in a simpler form. A simple process for risk assessment and management will also help to encourage all the appropriate people at work to participate in the risk assessment process.
Also, it is best that risk assessments are carried out by a group of suitably trained people rather than by one individual. This is because different people will often identify different hazards and risks and suggest different solutions to help keep workers safe and healthy. A team of trained risk assessors will therefore help to ensure that all the hazards and risks are spotted and assessed, and that the resulting risk controls are as effective as possible.
Risk assessment is one of the most important tools that we have for deciding how best to protect the health and safety of people at work, so we need to use it correctly.
By avoiding the pitfalls listed above, we should be able to produce quality risk assessments that help us to decide on the most effective ways of protecting the health and safety of our workers. We should also be able to give confidence and assurance to our senior leadership that the health and safety risks are being adequately controlled.
Suresh Tanwar is Head of audit and consultancy, British Safety Council (India) LLP
www.britsafe.in
FEATURES
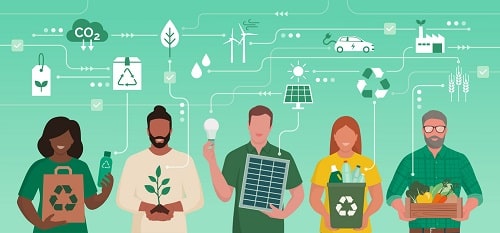
Changes to ISO management standards: start preparing now
By Dr Keith Whitehead, British Safety Council on 08 August 2025
The key ISO management standards setting out best practice frameworks for effectively managing occupational health and safety, environmental and quality risks and opportunities are undergoing major revision, so it’s essential businesses start planning now to meet the new requirements in order to maintain their certifications under the relevant standards.
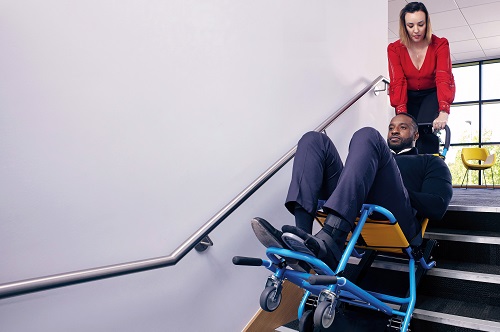
Inclusive, compliant evacuation planning: why training and maintenance matter
By Evac+Chair on 07 August 2025
Those responsible for business premises should provide assistive equipment to ensure the safe and efficient evacuation of people with mobility impairments. However, it is crucial that this equipment is regularly maintained and that staff are thoroughly trained in its use – otherwise, confusion and potentially fatal delays can arise in an emergency.
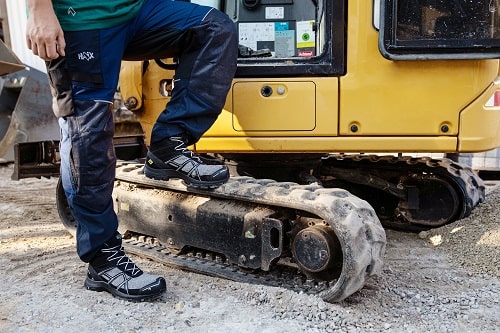
A step ahead: how the right safety footwear reduces workplace slips, trips and falls
By Simon Ash, HAIX on 06 August 2025
Safety footwear can prevent slip, trip and fall injuries, but it’s essential to consider other factors that could positively or negatively affect wearer comfort, such as breathable materials, waterproof qualities and boot weight.