Involvement in health and safety has changed Mhairi Cockburn’s plans for her future career. A Babcock apprentice specialising in welding at the company’s Rosyth dockyard, she became fascinated with the nature and role of health and safety in the business.
Features
Giving apprentices a voice
As a teenager, Mhairi wished to become a nursery nurse and studied childcare at a local college. After completing her training, she decided to continue her career in retail, while holding down a second job in security. At 28, she decided to make a complete career change. “I wanted to move outside my comfort zone and do something that I’d never done before. I decided to go to college and do my National Certificate in Fabrication and Welding. One of my college tutors highly recommended Babcock as an excellent place to work. At the time, I was looking for an apprenticeship in welding. Babcock was at the top of my list, so I was very pleased when I was offered the post there.”
Babcock’s Rosyth site is home to one of the largest waterside manufacturing and repair facilities in the UK, with a footprint of more than 300 acres. From here, the company supports a number of customers across the marine and nuclear sectors including the MoD, the Royal Navy, other international navies and commercial ship operators.
“I live some 20 miles away from Babcock’s Rosyth facilities, but I hadn’t seen the site up close before. When I visited it for the first time, I was amazed; I knew it was reasonably big, but I didn’t realise just how large it was and how vast some of the projects, such as the Queen Elizabeth Class aircraft carriers, are.
“At the beginning, the most challenging part was getting used to the new environment and the health and safety that goes with it, since I had never worked in an industrial environment before.”
Babcock’s apprentice scheme benefits both the company and the young people, says Mhairi. Photography: Babcock
Babcock’s Rosyth site has a safety, health and environment department and a suite of policies and procedures for each high-risk activity. The most common hazards are those associated with confined spaces and working at height.
Training courses are available to all employees on-site in relation to any tasks being undertaken. Health and safety boards display bulletins, toolbox talks and safety alerts across the site. Risk assessments and point of work safety assessments also play an important role in the site’s day-to-day business. There are also gold, silver and bronze levels of safety ‘passport training’, depending on what type of work staff are undertaking. All employees working on-site, including apprentices, must complete one of these levels.
“Babcock apprenticeship schemes are approximately four years long, depending on the individual’s progress. They prepare people for such roles as welder, fabricator, mechanical fitter and electrical fitter. My scheme is competency-based and I’m now at phase three. The apprentices attend college during phase one for 10 months, carrying out classroom and workshop based learning.
Early in the programme, they participate in the initial walk-rounds to familiarise themselves with the layout of the site and potential areas where they may end up working. All apprentices must achieve a passport level of safety training proportionate to the level of risk they will be facing.
“We also have to achieve a British Safety Council’s Level 2 Qualification in Health, Safety and Environmental Management to gain a silver passport, which is mandatory to enter a production area of the site. A gold passport must be gained for certain trades where workers carry out further training in working at height and confined spaces. I had to reach the gold level, which involved a week-long course. It taught me every aspect of health and safety, including possible on-site hazards and how they have been dealt with in the past.
Mhairi playing for Kirkcaldy ladies rugby club
“We receive a handbook, which was prepared by previous apprentices, and have a health and safety programme that includes safety spot checks, VLP (Visible Leadership Programme), walk rounds and health and safety assessments. We also spend several weeks on-site, particularly during college holidays.”
On completion of their first phase of training, apprentices move on-site to either a training centre or a production area. In the first two phases, they wear luminous yellow hats which make them easy to spot and make others aware that they are learning on the job.
In phase two of their training, apprentices spend a week in the health and safety office. This gives them an insight into all aspects of health, safety and environmental management. This also involves visiting various projects on-site with the designated safety officer. Apprentices meet all members of the team and learn about their roles and areas of operation. This includes audits, risk assessments, COSHH, policies, environmental management and certification.
“Apprentices are also invited to attend Forum Interactive sessions. These are drama-based behavioural safety sessions led by actors who show what could go wrong, what could have been done differently and what devastating consequences a wrong decision can have. One of our presenters was Louise Taggart, a Scottish health and safety campaigner whose brother died tragically in a work accident. We also watched presentations by people who have had an accident at work and spoke about their experiences.
“At the beginning of our training, we’re given the opportunity to join the Babcock Apprentice Safety, Health and Environment Forum, which gives apprentices an opportunity to contribute to health and safety matters across the site. The Forum meets every month and allows apprentices to meet members of senior management, the health and safety team and the trade union. We can raise any concerns we may have or suggest ideas and solutions. It’s very satisfying to follow an idea from start to finish and see the outcome of your initiative. I think that’s what really got me interested in health and safety.
“At the Forum, I took a lead on communications, which covered broad areas and included various pieces of creative work, as well as speaking to other apprentices. Andy Forbes, health and safety improvement director at Babcock, encouraged me to do this. I featured on one of the poster campaigns, which originated from the SHE Forum.
“Every year, a selection of apprentices and tradespeople are asked to complete the Safety Lens employee engagement survey, which is a Babcock International Group initiative. It has been created as part of the ‘Home Safe Every Day’ concept, which allows employees to speak frankly without being identified by name. In this anonymous survey, employees are asked to score five statements associated with each Babcock’s core value using a scoring system between 1 and 10, from strongly disagree to strongly agree. The results are collated and published. This helps the company to identify areas which need to be looked at and improved. Once action has been decided upon and taken, this is communicated back out to all employees in a ‘You said...we did’ format.
“I was involved in it as a facilitator. The survey is usually delivered by members of the senior management team or the safety team. However, it was suggested that I should deliver it to the apprentices because they might be more open to the message communicated to them by one their peers.”
Asked what she was most proud of, Mhairi said: “For my involvement in the Forum, I was nominated for the New Employee Award at Babcock’s annual Safety Excellence Awards 2018, for the marine sector. I travelled to Babcock, Plymouth for the Awards ceremony, along with the nominees in different categories from all the marine sites. I won the award for ‘my enthusiasm and commitment to health and safety’ and all the work I did for the Babcock Apprentice Forum.
“My involvement in health and safety made me realise that this area holds a great appeal to me. It was suggested that I may wish to start studying for the IOSH qualification before I complete my apprenticeship with the company.
“It was only after joining Babcock that I realised how important health and safety is, particularly in industry. I don’t think that many young people understand this. They think that health and safety is a paper exercise. That is why, in the future, I would like to work with young people and open their eyes to the nature of modern health and safety and its contribution to business.
“Babcock’s apprenticeship scheme gives young people an excellent grounding in this area, as well as many opportunities to get involved with it in different ways. It benefits both the apprentices and the company. For example, the Apprentice Forum allows them to look at health and safety with a fresh pair of eyes and suggest original ideas. This is a way of giving apprentices a voice in the company. After all, apprentices are the future.”
FEATURES
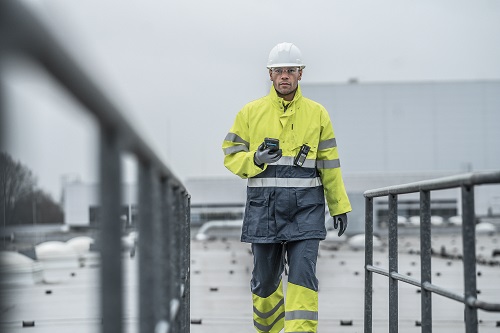
Gas detection – the rise of smart systems
By Becca Dodds, Draeger Safety UK on 26 August 2025
Mobile and fixed gas detectors have long been a crucial tool for alerting workers to the presence of asphyxiating or explosive gases, but developments in smart and connected technology are making it much easier to monitor entire networks of detectors and respond immediately to alarms and emergencies that could pose a risk to life or site safety.
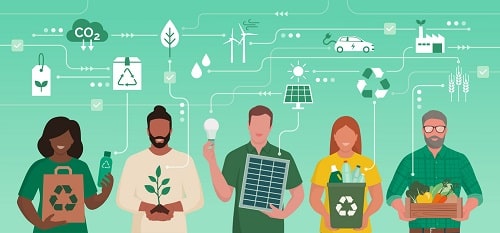
Changes to ISO management standards: start preparing now
By Dr Keith Whitehead, British Safety Council on 08 August 2025
The key ISO management standards setting out best practice frameworks for effectively managing occupational health and safety, environmental and quality risks and opportunities are undergoing major revision, so it’s essential businesses start planning now to meet the new requirements in order to maintain their certifications under the relevant standards.
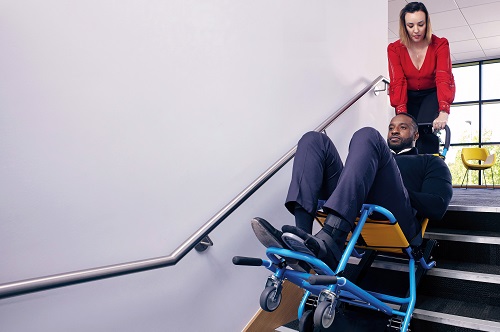
Inclusive, compliant evacuation planning: why training and maintenance matter
By Evac+Chair on 07 August 2025
Those responsible for business premises should provide assistive equipment to ensure the safe and efficient evacuation of people with mobility impairments. However, it is crucial that this equipment is regularly maintained and that staff are thoroughly trained in its use – otherwise, confusion and potentially fatal delays can arise in an emergency.