For over four decades, the EU has been the final safety net for workers in the UK. With their rights enshrined in EU law they knew that whatever domestic government policy objectives, there was a minimum standard below which their rights could not fall. This has not only cemented employment laws, but also workplace, product and industrial safety.
Opinion
Control means the ability to regulate effectively
While, understandably, the focus has been on employment law, let’s not forget the role of the EU in respect of safety regulation and standard setting. That underpinning is now at risk of being removed as ideologues drag us towards a Brexit that will do nothing for working people.
A crucial strand of that safety net is EU licensing laws. Chemicals and equipment must be approved to EU standards, usually through a single licensing body, such as the UK’s Chemical Regulation Division (CRD). It undertakes the bulk of the work to approve a new product, leaving another country’s own regulatory body with a simple tick-box exercise to ensure compliance.
Earning under £30,000 – the threshold proposed for EU migrants to earn before they’re granted a visa - does not make someone ‘low-skilled’.
When we leave, if we leave with a deal, we will have at least two years where all of our licensing will be performed by other countries. The current arrangements mean we will be effectively paying UK staff to do no licensing work for that period in the hope that they don’t leave. These are highly professional skilled people – is it really prudent to assume that they won’t be tempted by lucrative offers from private sector consultancies or other EU regulators, for example in Ireland? Processes are needed to ensure we maintain our capacity to make sure that the products, chemicals and equipment that our industry uses are fit for purpose and safe.
This becomes especially urgent if we leave with no deal. On 1 April, suddenly we will have to do all of our licensing and testing ourselves. One of the key aspects of No Deal planning has to be ensuring that we have the capacity to do this.
Uncertainty is a major problem for employers, those in charge of safety at work, and regulators. As I’m writing this we are less than two months from the Brexit deadline and we still don’t know what is going to happen. At the time of writing this, another vote on Theresa May’s deal was scheduled for Valentine’s Day and it is far from likely that the PM will get it through. What happens between then and when you read this article is anybody’s guess.
This uncertainty is amplified by the failure of the government to be clear about what its future immigration regime will look like, and how leaving the EU will impact our ability to recruit the people we need.
Despite the gravity of the situation, many politicians from across the spectrum continue to cling to myths about the EU. Conservatives steadfastly refuse to engage with the economic and social consequences of their immigration proposals. Business groups and unions are united in condemning these plans, especially the divisive salary threshold plan which would have a devastating effect in areas such as science and research. Earning under £30,000 does not make someone ‘low-skilled’, and all the evidence demonstrates that a threshold set at this level would deprive both public and private sectors of highly qualified talent from across Europe, and have a significant negative economic impact. This has particular implications for employers like the CRD, or Defra agencies as they strive to maintain capacity in difficult circumstances.
Brexit was driven by the slogan ‘take back control’ but there has been little recognition that ‘control’ in practice means the ability and capacity to regulate effectively.
Brexit was driven by the slogan ‘take back control’ but there has been little recognition that ‘control’ in practice normally means the ability, and crucially the capacity, to regulate effectively. Yet, still there has been a reluctance to recognise that taking back control of regulations must mean having regulators capable of enforcing them. It is a simple truth that disentangling the UK from EU regulatory agencies will mean that our own domestic regulators will need to expand their remits.
They will do so from a historically poor position. Years of funding cuts have left government agencies under-resourced and under-staffed for the challenge they now face. That is why we have seen crucial agencies such as the Office for Nuclear Regulation engaged in frantic recruitment drives in order to get enough staff in to fulfil their new responsibilities. But people skilled enough to act as nuclear safeguards inspectors, health and safety officers or chemical regulators do not simply grow on trees. Government will have to take a very different approach to recruiting and retaining skilled staff in these agencies in the years ahead. Regulation is not just about laws written in parliament, it is about people on the ground inspecting, enforcing, and ultimately protecting workers and the public.
Our preferred option is for the government to put its deal to the people, with remaining in the EU an option on that ballot. If that does not happen, we must leave with a deal, and the government must engage with unions at the same level as it engages with business groups on the manner in which we leave. Only then will we have a chance of safeguarding the rights and protections which enable us to work safely and with fair reward.
Mike Clancy is general secretary for Prospect, the union for professionals
OPINION
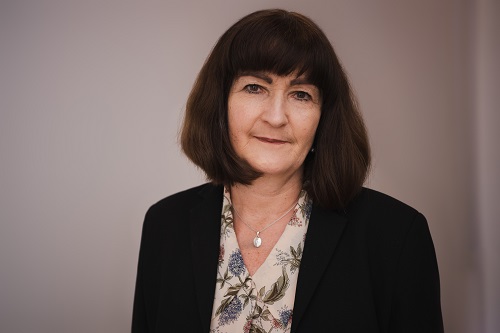
Battery Breakdown e-bike fire safety campaign: where are we two years on?
By Lesley Rudd, Electrical Safety First on 03 July 2025
The Product Regulation and Metrology Bill currently before Parliament offers the opportunity to reduce the fire risks posed by sub-standard e-bikes, e-scooters and their lithium-ion batteries, but the Government needs to go further and faster to protect public safety.
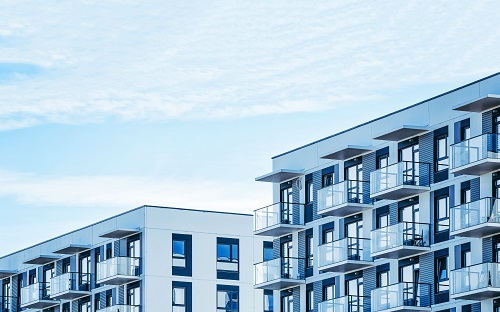
The building safety crisis: a year of Labour in power, still no end in sight for leaseholders
By Campaign team, End Our Cladding Scandal on 01 July 2025
It’s a year since Labour came to power with manifesto commitments to fix the failed approach to the cladding and building safety scandal and deliver meaningful change.
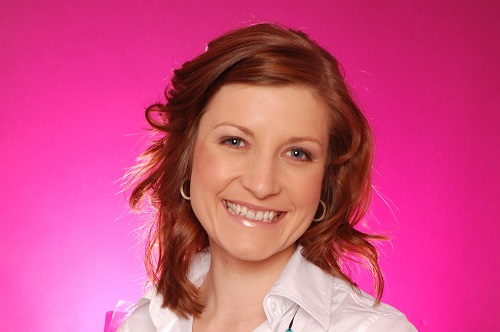
Rethinking workplace wellbeing for a new era
By Kate Field, BSI on 16 June 2025
Today’s workers increasingly value the flexibility to pick the most suitable working model for their needs – whether this be hybrid, fully remote or site-based. However, new BSI research shows a more important consideration is working for an organisation that genuinely prioritises employee wellbeing, offers development opportunities and encourages staff autonomy.