Tests show a significant amount of safety footwear on the UK market does not perform as advertised, potentially putting workers at risk of serious injury, but there is a quick way to check the products you purchase meet the required standard.
Features
Running into problems with safety footwear
Quality safety footwear is vital for workers across a range of industries. As the Health and Safety Executive observes, the feet and legs are prone to a range of hazards including temperature, electrostatic build-up, slipping, cuts, falling objects, heavy loads, metal and chemical splash, and being crushed or struck by a vehicle.
If a workplace health and risk assessment determines that personal protective equipment (PPE) is required, health and safety law stipulates that it must be adequate for the hazard and suitable for the wearer, the task and the environment. Workers might require footwear that is anti-static, electrically conductive or resistant to penetration. It may also need to offer high levels of slip-resistance or protect against extreme heat or cold.
Only five of the 42 footwear products tested by BSIF between December 2021 and December 2022 were found to be fully compliant. Photograph: Satra.
With the potential severity of many of these hazards in mind, it is alarming that a significant proportion of the safety footwear on the UK market currently fails to perform as advertised.
British Safety Industry Federation (BSIF) testing has found that an incredible 88 per cent of products that it tested from suppliers not signed up to our Registered Safety Supplier Scheme (RSSS) showed failures against product performance claims and/or the required supporting documentation. Only five of the 42 footwear products tested between December 2021 and December 2022 were found to be fully compliant.
UK requirements
Manufacturers, importers, distributors, internet sellers and agents involved in the supply of PPE have clear legal responsibilities and obligations in the UK. Safety footwear used at work must comply with Regulation (EU) 2016/425 for PPE and follow the relevant approval procedures to qualify for a UKCA or CE mark.
The regulation states that safety footwear must meet the standards specified by BS EN ISO 20345. This standard identifies the basic and optional requirements for general purpose safety footwear, including slip resistance, mechanical and thermal risks and ergonomic behaviour.
Footwear might also need to conform to other relevant standards, such as BS EN ISO 20347: Personal Protective Equipment – Occupational Footwear or BS EN ISO 20349-1: Personal Protective Equipment. Footwear Protecting Against Risks in Foundries and Welding – Part 1.
Safety shoes designed to protect against anything more than minor injury are classified as Category II or III. These products must undergo a type-examination by an accredited testing body to ensure they meet their ‘Essential Health and Safety Requirement’ (EHSR). Category III products, which protect against permanent damage and death, additionally require ongoing independent quality assurance through either Module C2 Product Verification or Module D Product Quality Assurance.
Alan Murray is chief executive of British Safety Industry Federation (BSIF)
Manufacturers are obliged to provide the Declaration of Conformity along with user instructions and technical documentation to sell and distribute Category II and III safety footwear in the UK.
Employers have a duty of care and are responsible for ensuring that the PPE they provide for their workers is properly certified and approved, too. Not all buyers and specifiers are aware of this responsibility – and very few will have all the knowledge or resources they need to validate suppliers’ claims.
Product failures
The lack of market surveillance and enforcement in the UK means it can be difficult to distinguish responsible suppliers from less responsible ones. Furthermore, the quantity of non-compliant products being sold in the UK market is on the rise.
Some products claim UKCA or CE approvals but have not been appropriately certified. These products should not be used by businesses because they contravene safety legislation. Also, because these items generally do not perform as they should, they pose a risk of serious injury to wearers as well as exposing businesses to the risk of prosecution for failing to protect their staff by providing them with non-approved, non-certified PPE that does not provide adequate protection from injury.
Our tests on non-Registered Safety Supplier Scheme products uncovered some disturbing failures. For example, there has been a proliferation of so-called safety footwear that is often promoted as ‘unbreakable’ or ‘indestructible’ on social media. These products all too often have not been tested or accredited to any of the required standards and failed many of our tests.
Any products that claim to have a protective midsole should be able to prevent a nail going through the base of the footwear at a force of 1,100 Newtons. However, none of the so-called ‘indestructible’ products we tested did so. Many products also failed the compression tests or had steel toecaps that were not produced with the correct shape or to the standards required.
Registered Safety Supplier Scheme
The BSIF works hard to eliminate unsafe, non-compliant and illegal safety footwear from the UK (and where possible, international) market.
Members of our Registered Safety Supplier Scheme must sign a formal, binding declaration that all PPE they offer meets the appropriate standards, fully complies with the PPE regulations and is correctly UKCA or CE marked. Every year, we source one item of PPE from each member for assessment by an accredited test laboratory.
We tested 108 items of safety footwear produced by RSSS members between December 2021 and December 2022. Whereas 88 per cent of non-member products tested failed, 90 per cent of member products met all requirements on product claims and documentation. RSSS members whose products failed to meet the test criteria were required to rectify issues immediately to remain part of the scheme. If a member ever refuses corrective action they are removed from the scheme and referred to the authorities.
This is why the BSIF always recommends that all UK buyers and specifiers of safety products and PPE look for the Registered Safety Supplier Scheme Shield. Although ensuring safety footwear is fully compliant with all required standards can be hugely challenging, by using a Registered Safety Supplier businesses can be confident that they are getting genuine, appropriately approved products that perform as they should.
Therefore, we encourage all those charged with specifying PPE to:
- CHECK the supplier is a member of the BSIF’s Registered Safety Supplier Scheme. BSIF-audited suppliers are compliant, competent and trustworthy. Don’t settle for less.
- SELECT appropriate, certified and compliant products. Registered Safety Suppliers can support the product selection process through their competence, capability and knowledge.
- PROTECT your workforce and your business. Registered Safety Suppliers go above and beyond, helping to keep your people safe and helping your business to thrive.
Alan Murray is chief executive at British Safety Industry Federation (BSIF).
A full list of registered suppliers is available at: bsif.co.uk/rsss
FEATURES
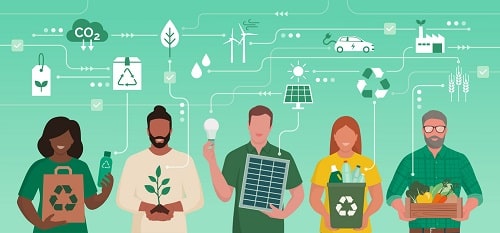
Changes to ISO management standards: start preparing now
By Dr Keith Whitehead, British Safety Council on 08 August 2025
The key ISO management standards setting out best practice frameworks for effectively managing occupational health and safety, environmental and quality risks and opportunities are undergoing major revision, so it’s essential businesses start planning now to meet the new requirements in order to maintain their certifications under the relevant standards.
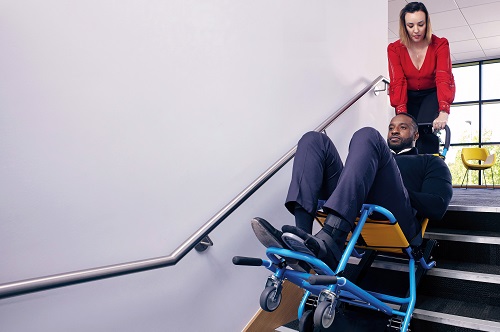
Inclusive, compliant evacuation planning: why training and maintenance matter
By Evac+Chair on 07 August 2025
Those responsible for business premises should provide assistive equipment to ensure the safe and efficient evacuation of people with mobility impairments. However, it is crucial that this equipment is regularly maintained and that staff are thoroughly trained in its use – otherwise, confusion and potentially fatal delays can arise in an emergency.
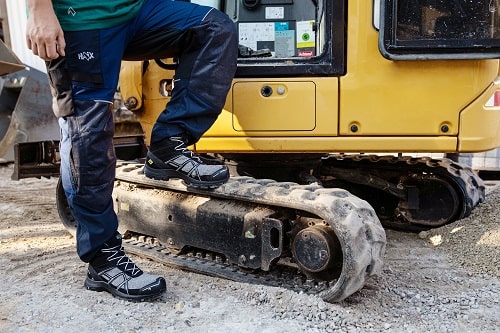
A step ahead: how the right safety footwear reduces workplace slips, trips and falls
By Simon Ash, HAIX on 06 August 2025
Safety footwear can prevent slip, trip and fall injuries, but it’s essential to consider other factors that could positively or negatively affect wearer comfort, such as breathable materials, waterproof qualities and boot weight.