Environmental, safety and health software can greatly improve the management of EHS risks and bring wider business efficiencies, but it’s essential to select the right system – and ensure everyone buys into its correct and full implementation.
Features
EHS software: a vital tool for improving safety at work
What is EHS software?
In recent years, the environmental, health and safety (EHS) software market has seen notable expansion and consolidation, propelled by rising demand for EHS solutions, investment and industry starting to fully embrace Industry 4.0 (known as digital transformation).
The positive growth and sustained upward trajectory have spurred competition, leading to numerous instances of acquisitions, investments and asset sales linked to EHS software.
Considering the aforementioned factors, embracing an Industry 4.0 future is inevitable, and the transition from legacy Excel-based control of processes and information will accelerate significantly in the coming years.
Photograph: iStock/Jay Yuno
So, what is EHS software and why might a business need it? EHS software is a group of digital module solutions adopted by companies to oversee regulatory compliance, manage enterprise risk and handle corporate sustainability data and initiatives.
Implementing EHS software enables companies to fully embrace Industry 4.0 through streamlining operations, mitigating risks and proactively preventing undesired events. This will ultimately save time and resources and, most importantly, prevent injuries and fatalities.
EHS software is typically made up of a mix of the following digital modules/key areas:
- Safety Management
- compliance with safety regulations; functionality to support behaviour-based safety and job hazard/safety analysis; functionality for safety meetings and objectives management; lone worker safety
- Control of Work
- risk assessment; isolations management; permit to work; mobile, in-field technology
- Incident Management
- track, manage and analyse incidents; facilitate corrective and preventative actions
- Audit and Inspections Management
- scheduling of EHS audits; import, create and change checklists for EHS audits
- Chemicals Management
- database for safety data sheets (SDS); SDS content to be viewed on the web or mobile app; chemical incident management workflows can be configured
- EHS Compliance and Risk Management
- functionality to provide risk identification and risk assessments; maintenance of an operational risk register; emergency response management
- Management of Change (MoC)
- functionality to handle MoC workflow and approvals; ability to integrate the MoC process with other software
- Mobile Solutions
- in-field risk assessment; real time measurement; in-field isolations; offline capabilities; image capture
- Training
- established EHS training modules; e-learning; ability to track and log training progress.
There are of course other elements to EHS software and the utilisation of these including the ones above will vary from business-to-business. There are lots of options, but the key is to adopt those options that best suit your business, current infrastructure and legacy systems.
Emma Bundy is head of marketing at Yokogawa RAP
Why is EHS software important?
An effective EHS software platform allows businesses to:
- Digitally monitor, track and analyse real-time data across several different streams and workflows
- Instantly streamline and report on this data allowing for adherence to site protocols and legislation
- Implement timely corrective action
- Significantly improve communication.
With this functionality comes several benefits – not just for site safety but also for site efficiencies, improved authorisation, monetary savings and the ability to continuously improve.
This is achieved by digitising work processes and automating workflows, which can significantly enhance overall productivity, providing a business with a robust digital platform to build on for the future.
However, a crucial aspect of this transition lies in the ability of diverse systems to talk to one another.
Interoperability capabilities of systems
Individual siloed solutions are not adequate to fully realise the breadth and depth of benefits available. Hence, selecting the right software provider becomes paramount, along with ensuring acceptance by the IT department within an organisation.
One of the best ways to overcome internal IT barriers is to adopt a system that can communicate both ways with legacy or future systems. EHS software systems are now available that use certified APIs, which allow all of an organisation’s operational systems and technology to interact and generate the required actions with the company’s new digital EHS safe systems of work (SSoW).
Furthermore, it’s crucial for the IT department to be aligned when introducing EHS software, because the EHS platform impacts all areas of a business. With this in mind, it’s therefore also essential to secure buy-in for the new software across the entire company, as this will help ensure the software is fully accepted and utilised as rapidly as possible so the benefits can be quickly realised and a timely return on investment (ROI) is achieved.
The importance of leadership in safety
However, all the above can only be achieved if the initiative comes from the top down and there is a dedicated team to lead the implementation and continuously communicate the reasons and the benefits.
The front-end implementation of any digital system is key to its successful rollout and this is even more important when a new safety software system is being installed that will hopefully change the company’s safety culture for the better. This means having the right people in the right place, with the right motivation to explain and introduce the system to the workforce and ensure its acceptance and successful rollout.
When EHS software is successfully implemented it facilitates continuous improvement initiatives across the business. With real-time visibility of work and the improved communication capabilities of a digital system, improvement actions can be quickly implemented, benefiting not only the safety of the site and workforce, but also the organisation’s efficiency.
It must be emphasised again, though, that the implementation and successful use of the new system following its rollout can’t be a standalone health and safety department initiative. The overall success of the software must be driven from the CEO down and the new digital system must become a fundamental way of safe working.
This commitment, along with selecting the most suitable EHS software solutions, can certainly help achieve a step-change in EHS performance.
Where does digital Control of Work (CoW) fit in?
The concept of Control of Work (CoW) (i.e. robust identification and control of risk, isolations management and permits to work), originated from the oil and gas, chemical and mining industries following disasters such as Seveso, Piper Alpha and Bhopal. Following these incidents, it became clear that high hazard industries needed tighter regulation and control to prevent future unnecessary deaths and injuries to workers.
As digital CoW solutions (i.e. software-led systems) are becoming increasingly prominent and simpler to deploy, the demand for CoW software will inevitably extend beyond high-hazard sectors into other industries. In fact, the market forecast for CoW solutions is already indicating a growing need for robust CoW solutions across many different industries and levels of hazards.
Photograph: Yokogawa RAP
As with all technology, the functionality and scope of CoW software is continuously improving and expanding. This is leading to improved system interoperability (the ability for EHS software to seamlessly link with other business software systems), and the growing use of real-time data streams to monitor people and assets, identify potential incidents, mitigate risks, close the loop on corrective actions and improve operational safety and efficiency.
The growing requirement for interoperability between EHS software and other business software systems, and the increasing desire for organisations to integrate all their safety systems, policies and procedures, means CoW software will increasingly become a key element within a company’s overall EHS system.
What is Industry 4.0 and 5.0?
With the next era of EHS digital strategies being driven by integrated software systems, companies are likely to use several solutions, tools and devices to manage their EHS processes and potentially redefine their EHS strategies.
For instance, a lot of companies are already considering how to link IT (information technology) and OT (operational technology) solutions, and this means EHS software providers are increasingly addressing both client hardware and software needs with the aim of significantly streamlining processes (such as identification of task, isolation, assessments and consent) for the maximum benefit and safety of the client’s workforce, site and reputation.
So, with Industry 4.0 offering the digital tools to allow all of the above, what is industry 5.0 and what is it likely to mean for the future of safety?
According to the European Commission, “the next step (Industry 5.0) is to place the wellbeing of the worker at the centre of the production process and to use new technologies to provide prosperity beyond jobs and growth, while respecting the production limits of the planet”.
So, the future is not just about technology and devices but rather how well we can interconnect a worker with their environment and to the tools and other workers who are with them. And what does a future worker look like? In truth, the workforce of the future will be both humans and machines working in harmony together.
Emma Bundy is head of marketing at Yokogawa RAP.
For more information see:
T: +44 (0)1792 341343
FEATURES
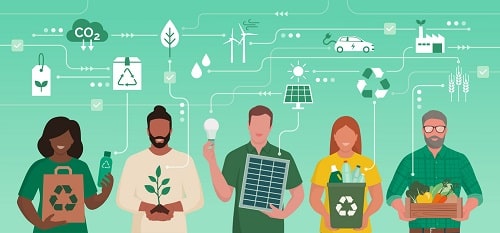
Changes to ISO management standards: start preparing now
By Dr Keith Whitehead, British Safety Council on 08 August 2025
The key ISO management standards setting out best practice frameworks for effectively managing occupational health and safety, environmental and quality risks and opportunities are undergoing major revision, so it’s essential businesses start planning now to meet the new requirements in order to maintain their certifications under the relevant standards.
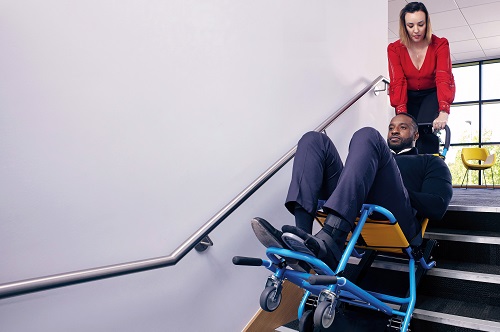
Inclusive, compliant evacuation planning: why training and maintenance matter
By Evac+Chair on 07 August 2025
Those responsible for business premises should provide assistive equipment to ensure the safe and efficient evacuation of people with mobility impairments. However, it is crucial that this equipment is regularly maintained and that staff are thoroughly trained in its use – otherwise, confusion and potentially fatal delays can arise in an emergency.
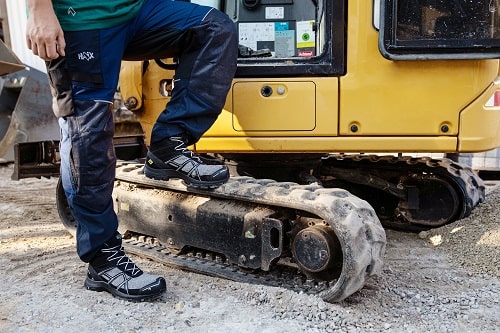
A step ahead: how the right safety footwear reduces workplace slips, trips and falls
By Simon Ash, HAIX on 06 August 2025
Safety footwear can prevent slip, trip and fall injuries, but it’s essential to consider other factors that could positively or negatively affect wearer comfort, such as breathable materials, waterproof qualities and boot weight.