Accredited providers of materials handling equipment operator training have to meet certain requirements and are subject to adequate auditing, and this provides assurance that the training will be delivered to the correct standard.
Features
Training time: why accreditation is key
Because they are big, expensive and potentially very dangerous, forklift and warehouse trucks command the highest levels of attention when it comes to ensuring a safe working environment. And in order for employers to fulfil their duty of care for safety, it’s vital that all involved are equipped with the insights and skills to ensure ‘it could never happen here’.
A common denominator in almost every forklift accident is insufficient or improper training. Operating a forklift is not as simple as driving a car; it demands a specialised skill set that can only be acquired through comprehensive training.
A common denominator in almost every forklift accident is insufficient or improper training. Photograph: AITT
Moreover, the wider that knowledge pool among staff, the fewer the risks. Safety systems, such as segregation through the use of walkways, warning signs and traffic routes are all important, but at the very heart of safe operations is high quality and across-the-board training.
The quality comes from ensuring the provider meets the highest standards. The breadth is achieved by extending training well beyond those who operate the equipment.
Great care is necessary when selecting a training provider as the sector is largely unregulated. Indeed, perhaps the only reliable way of ensuring a high standard of training is by using an accredited provider. This will deliver the traceability, consistency and the assurance of best practice... along with the certainty that the training provider is up to date with standards and using the latest resources. This is important because, surprisingly perhaps, the categories for training do change over time as do the training materials.
Top to bottom training
It’s a truism to say that a company culture starts with management leading by example. That is never more so than when it comes to safety. Supervisors and management should, of course, follow all rules and guidelines as it sends a strong message and emphasises the importance of safety in the workplace.
More than that, it is also incumbent on anyone overseeing materials handling operations to understand their role. Without the knowledge and competence to evaluate what constitutes safe and efficient working practices how can anyone manage operations effectively? That’s not the same as learning how to operate a forklift but it does mean becoming conversant with best practice. The good news is that short courses are available (some online) to arm you with the capability, confidence and credibility to challenge poor practice and recognise – and reward – excellence.
Great care is necessary when selecting a training provider as the sector is largely unregulated. Photograph: AITT
So far so good, but training needs to go further still.
Ask anyone who has had any experience of a forklift accident and they will share how deep and far-reaching the consequences for all involved. As well as the family of the victim it can impact heavily on colleagues and general company morale. That’s why engaging the materials handling safety message at every level makes such a profound difference. After all, around two-thirds of accidents involve those working on foot in close proximity to these large, powerful and unforgiving machines.
A really effective way to embrace and extend a safety culture is an awareness workshop involving both operators and pedestrians. It’s a remarkably powerful opportunity for all parties to exchange experiences, share insights and air concerns. Gaining a better understanding of each other’s expectations and seeing things from a fresh perspective invariably results in far clearer communication (especially where trucks and people interface) and can forge much stronger bonds between colleagues.
Liam Knight: "A really effective way to embrace and extend a safety culture is an awareness workshop involving both operators and pedestrians." Photograph: AITT
How accreditation makes a difference
Let’s be clear. Accredited training will never be the cheapest… but it will always be among the best.
As the checklist below confirms, accredited training is unrivalled when it comes to ensuring the outcomes you need whilst also delivering value for money.
The benefits for an operator trained to the standards demanded by an accredited instructor include enhanced awareness, extra confidence and greater productivity.
The advantages for employers are perhaps even greater. Accredited training guarantees:
- Traceability through accurate and instantly accessible records
- Courses that are continuously updated and in line with the latest standards
- Use of the very latest resources including manuals, handbooks, guides, etc
- Regular auditing to ensure trainers are following best practice
- Training that keeps pace with sector changes to equipment, classification, etc
- Independent verification
- Evidence of best practice in the event of a HSE inspection.
In-house training and recruitment
If your operations require in-house trainers to keep pace with changes or to meet short deadlines you can still enjoy many of the benefits associated with accreditation by joining as a member of AITT, including access to vital resources such as up-to-date test sheets for all categories of equipment.
As an employer, working with an accrediting body like AITT brings an important additional benefit when it comes to recruiting new staff. Rather than take an applicant’s training certificates at face value (there are some very convincing forgeries in circulation) working with an Accrediting Bodies Association (ABA) member such as AITT provides access to online databases where you can check the validity of documentation instantly, at any time of day or night.
Importantly, by choosing an accredited training provider, you can be safe in the knowledge you’ll never work alone.
For more information see: aitt.co.uk
Liam Knight is Managing Director at AITT
FEATURES
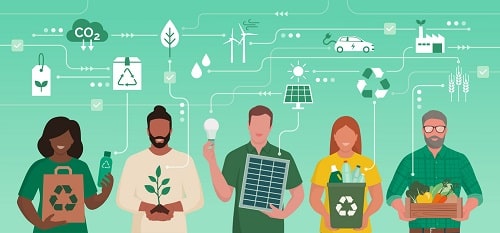
Changes to ISO management standards: start preparing now
By Dr Keith Whitehead, British Safety Council on 08 August 2025
The key ISO management standards setting out best practice frameworks for effectively managing occupational health and safety, environmental and quality risks and opportunities are undergoing major revision, so it’s essential businesses start planning now to meet the new requirements in order to maintain their certifications under the relevant standards.
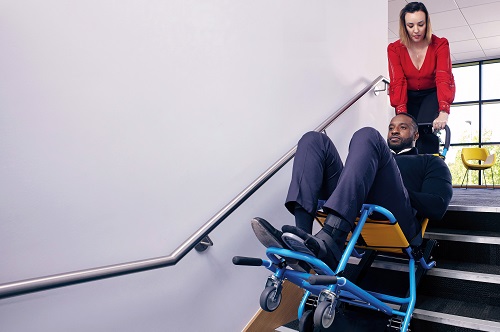
Inclusive, compliant evacuation planning: why training and maintenance matter
By Evac+Chair on 07 August 2025
Those responsible for business premises should provide assistive equipment to ensure the safe and efficient evacuation of people with mobility impairments. However, it is crucial that this equipment is regularly maintained and that staff are thoroughly trained in its use – otherwise, confusion and potentially fatal delays can arise in an emergency.
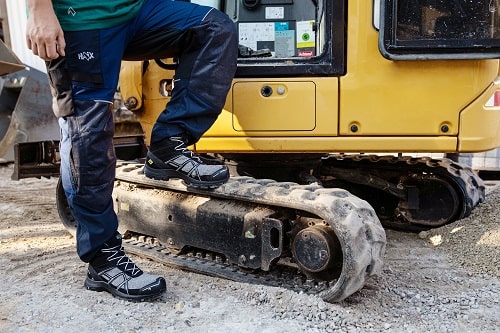
A step head: how the right safety footwear reduces workplace slips, trips and falls
By Simon Ash, HAIX on 06 August 2025
Safety footwear can prevent slip, trip and fall injuries, but it’s essential to consider other factors that could positively or negatively affect wearer comfort, such as breathable materials, waterproof qualities and boot weight.